MARK GORMAN:It's a massive machine, but it's a real piece of precision engineering too.
MARK GORMAN:From the moment we launch the kit to make the first internal module right through to the engine being dispatched, it's 20 days.
NARRATOR:'The Trent 700 jet engine is Rolls-Royce's biggest seller, and has so far clocked up 13 million flying hours in just 15 years.'
NARRATOR:'As a commercial company, it's essential the Rolls-Royce production line runs like clockwork.
MARK GORMAN:It carries a payload of 242 tonnes, at 37,000ft, for 9,500 miles,
MARK GORMANHEAD OP PRODUCTION & TESTING
MARK GORMAN:which, as you can imagine, is a serious challenge for any technology to deliver. So it really is at the high end of manufacturing and assembly.
NARRATOR:'The popularity of the Trent 700 is also the factory's biggest challenge.
NARRATOR:'With orders placed to build 400 new engines, the company has to produce at least four a week.For their production line, one of the most complex in the world, time is big money.'
NARRATOR:'Each Trent engine is built from modules, eight separate sections which are put together on the assembly line.
NARRATOR:'But each module is made from thousands and thousands of components,
NARRATOR:'and the monumental task of gathering them starts here, at the massive parts warehouse.'
NARRATOR:'Kevin Carr's job is to make sure every engine part is delivered to the assembly line on time.'
KEVIN CARR:On average, with my pedometer, I average about eight miles a day.
KEVIN CARR:On an average day, but if we have lots and lots of issues my best is just under 16 miles in a day.
KEVIN CARR:Lots and lots of shoe leather used.
NARRATOR:'This is called JIT, or just in time, technology. Essentially, this means the production process is managed to a timescale, and that parts are dispatched when needed, and not sitting on the shelf for any length of time.'
KEVIN CARR:I do know the guys around here say just give me a part or show me a box and can tell you what it is and where it goes.
KEVIN CARR:Everything's footprinted ready for the guys, it's a bit like a sweet shop for them, they can pick and choose what they want.
KEVIN CARR:We supply the very first nut, bolt or washer that they fit, right up to the very last little bit of plastic that we put on the engine before it goes out the door to the customer. So that could be anything up to 30,000, 40,000 parts, depending on which engine it is.
NARRATOR:'It's Kev who kicks off every new engine build. Two days before the assembly begins, he triggers the dispatch of tens of thousands of parts from the warehouse.'
KEVIN CARR:Have they got all the bits there for it?
WAREHOUSE EMPLOYEE:Yes.
KEVIN CARR:Got all the paperwork?
WAREHOUSE EMPLOYEE:Yes.
KEVIN CARR:Yeah, so we're all ready to go, then. OK, thanks very much.
KEVIN CARR:Looking at the boxes, you wouldn't know,but just looking at the odds and sods if they're lying on the floor there's nothing under a thousand pounds.
KEVIN CARR:You've got the engine control management unit, roughly three quarters of a million pounds worth in that box, just sitting there on a pallet.
KEVIN CARR:Anything up to two hundred million pounds worth of stock on the shelf. We have roughly five engines worth of stock of anything.
NARRATOR:'For the assembly process, industry has employ effective and innovative management when planning production, to ensure the smooth running of the build. After all, time is money.'
Video summary
Rolls Royce use 'just in time' production planning for the Trent 700 jet engine.
This saves time and money. This is the production process on a big scale.
Planning the production process is key and teamwork is essential. JIT -'just in time' production is used to stop parts being over-ordered, taking up space and costing the firm money.
Clear plans and timescales are crucial: In industry, time is money.
Teacher Notes
Could be used to introduce learners to the principles of just-in-time (JIT) manufacture.
Learners could list the advantages and disadvantages of JIT for manufacturers.
Students should develop an understanding of how products are manufactured to different scales of production, including one-offs, batch, mass, continuous, just-in-time.
They could be given a list of products and asked to determine which production method is most appropriate, giving reasons for each choice.
Another aspect that might be discussed is the use of ICT to manage the logistics of a just-in-time production line.
This clip will be relevant for teaching KS3 and KS4/GCSE Design and Technology, materials.
This topic appears in OCR, Edexcel, AQA, WJEC in England and Wales, CCEA in Northern Ireland and SQA National 4/5 and Higher in Scotland.
Building a supercar. video
Formula One team McLaren show us the production floor of their supercar, the MP4-12C.
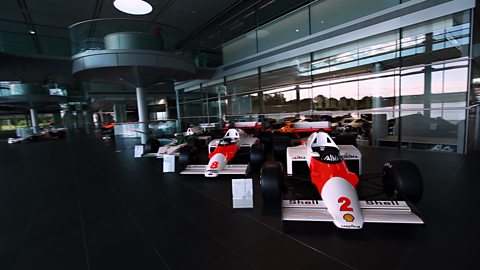
How satellites survive in space. video
A thermal architect explains how satellites are designed.
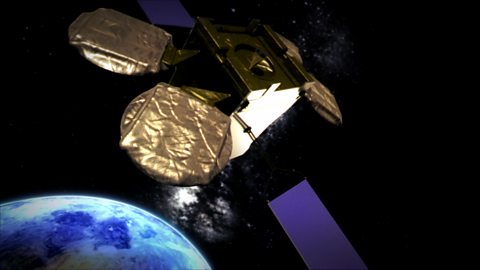
How car designers are inspired. video
An insight into design inspiration that has influenced the production of a sports car.
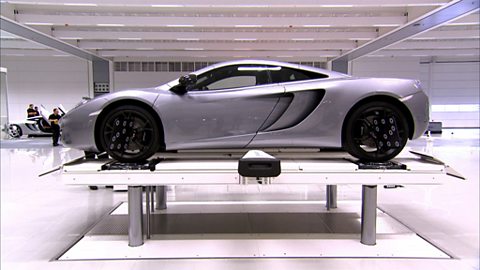